【倉庫業務改善】精度の高い時間計測で生産性アップ
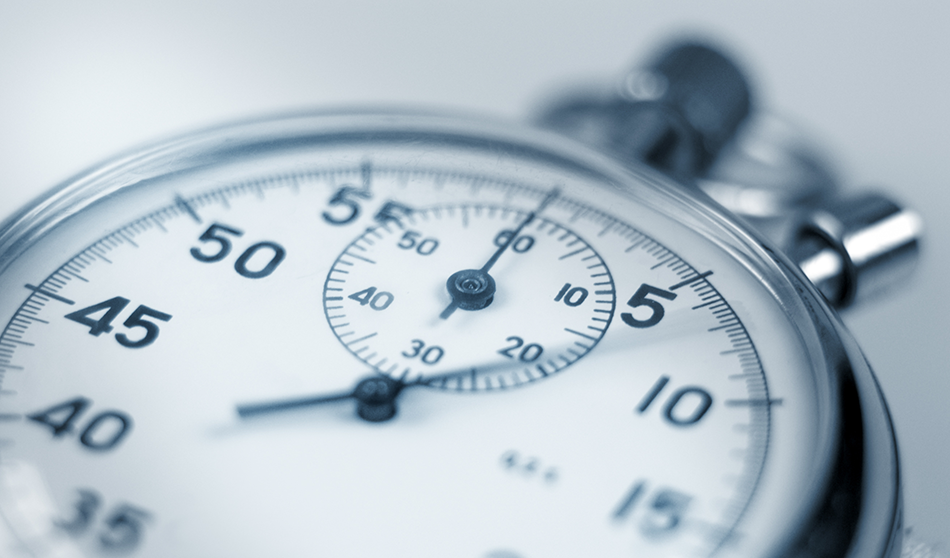
物流事業者A社が荷主B社より保守パーツセンターの業務を受託してから半年が経ちました。ようやく業務が安定的に稼働するようになりほっとしたのも束の間、B社より「更なる作業効率化を進めるように」と強く要請されています。B社は「KPIを取るように」とも要求してきていて、担当者であるCマネージャーはどのように取り組めばよいのか困ってしまいました。
B社が要求してきているKPIというのは、「Key Performance Indicators」を略したもので「重要業績評価指標」と訳されています。要するに、目標の達成度を数値で表現したものということになります。本来、目に見えない状態を数値化して目に見えるようにしているわけです。
■倉庫業務でよく利用されるKPI=人時生産性とは?
倉庫であればKPIとして人時生産性がよく利用されています。人時生産性とは作業者1人1時間あたりの作業量ですから、作業量÷作業時間数で計算されるもので、ピッキングや仕分けなどの作業の生産性を測定する指標です。
具体例で説明してみましょう。ピッキングの作業量が5,000行あったとして、作業員5名が10時間かけて処理していたとすれば、人時生産性は5,000÷5÷10=100行/時間ということになります。その後、倉庫作業を改善したところ同じ作業量を5名、8時間で処理できるようになりました。そこで、人時生産性を再度計算してみると5,000÷5÷8=125行/時間になります。比率で表すと125÷100=1.25つまり125%ですから、人時生産性は改善によって25%アップしたことになります。
■人時生産性を計算する場合の落とし穴
さて、このような計算を実際に行ってみると、人時生産性が思いのほか高いことがあります。高い数値が出ることは望ましことなのですが、どうも実感と合っていないのです。実はここに落とし穴があります。
人事生産性を計算するためには作業量のデータと作業時間のデータが必要です。作業量のデータはWMSから正確な数値を取得することが可能です。しかし、問題は作業時間のデータなのです。
よくやる間違いなのですが、例えば、時間データとしてハンディターミナルで計測した数値を利用したとすると、ハンディターミナルで測定できる時間だけが参入され、測定できないピッキングの準備作業などの時間が漏れてしまいます。そうすると分母となる作業時間数が本来の数値よりも小さくなりますから、人時生産性が大きくなってしまうのです。
先ほどの具体例でいえば、本当は5名が10時間かけてやっているはずなのに、ピッキング準備作業にかかった2時間が漏れていたために、計算は5,000÷5÷8=125行/時間となり、人時生産性はアップしているように見えます。しかし、実際はピッキング準備作業にかかった2時間も加えなければなりませんから、正しくは5,000÷5÷10=100行/時間であり、人時生産性はまったく改善していません。
B社が要求してきているKPIを正確に計算するためには、ピッキングの準備作業も含めた作業時間全体を精度よく計測しておく必要があります。
※作業時間全体をスマホで精度よく計測できるツール「ろじたん」についてはこちら
■作業時間の全体を精度よく計測してみると・・・
物流事業者A社のCマネージャーは準備作業およびロケーション別の作業時間を正しく把握することにし、計測のための作業リストを下記のように細かく設定して計測してみました。
1週間計測し、そのデータを集計してみると意外な事実が分かってきました。それは、事前に想定していたよりはるかに事務作業や準備作業といった付帯作業の比率が高かったのです。それは裏を返せば、ピッキング作業や入庫作業などの主体作業の比率が低いということを意味しています。
なお、付帯作業というのは
・主体作業を間接的にサポートするための作業
・実施しなくても何とか倉庫営業が行える作業
を指します。これに対して、
・顧客より収受する料金に直結した付加価値がある作業
・実施しないと倉庫営業が行えない作業
・作業品質を担保するために実施すべき作業
を主体作業と呼びます。さらに、
・顧客より収受する料金とは直接関係ない作業
・実施しなくても倉庫営業が行える作業
のことを不稼働作業といいます。
一般的には、付帯作業や不稼働作業の比率を低くし、主体作業にかける時間の比率を高めていくことで倉庫の生産性を向上させることができます。つまり、物流事業者A社では、これまで倉庫の生産性がかなり低かったことがはっきりしたわけです。
そのことはCマネージャーにとっても他のスタッフにとってもショックでした。しかし、データによって、これまでなんとなく感覚的に感じていたことが数値化されたことで改善のための議論が始まり、スタッフからも自主的に改善アイデアが提案されるようになりました。
■次々と改善策を実行に移す!
精度の高い計測データをタイムチャート化してみると様々な改善策が浮かび上がってきます。
例えば、スタッフからは「後工程に貢献の少ない準備作業を削減しましょう。」とか「時間のかかるロケーションのレイアウトは見直すべきです。」といった有効な改善策が提案され、Cマネージャーは次々とそれらを実行に移していきました。
もちろん、改善策を実行するだけでなく、同時に作業時間全体を精度よく計測することも忘れず定期的に実施していきました。
■荷主B社より信頼を獲得し、新たな業務の受託成功!
Cマネージャーを中心とした改善活動によって準備・仕分けなどの付帯作業から、ピッキングや検品などの主体作業に作業内容がシフトしていきました。下のグラフは9月から11月にかけての作業構成の変化を表しています。
全体の生産性は向上し、こうした継続的な改善活動が荷主B社によって認められ、物流事業者A社はB社から新たな業務を受託することにも成功したのです。
■まとめ
倉庫作業を改善し生産性をアップさせるためには、なんとなく感覚的に問題を捉えるだけでは足りません。きちんと数値化し、原因を突き止めることが重要です。そのためには、作業時間を精度よく計測することが欠かせません。精度の高い計測データをグラフやチャートで見える化すれば、スタッフの改善意欲をも引き出すことが可能なのです。
「ろじたん」とは、スマホアプリとWebの連携により、倉庫内の作業時間を計測するツールです。
掲載記事・サービスに関するお問い合わせは
お問い合わせフォームよりご連絡ください
株式会社NX総合研究所が書いた記事
この記事の関連タグ
関連する記事
-
ブログ / 519 viewsアサーション:物流現場でも使えるコミュニケーションスキル
「アサーション」とは、「自分も相手も大切にする自己表現」で「自分の考え、欲求、気持ちを、率直に、その状況にあった適切な方法で伝えるスキル」です。 アサーションを…
-
ブログ / 1,448 views物流案件を進める上で必要なプロジェクト・マネジメント スキル
プロジェクト・マネジメントに有効なスキルツール、主には①プロジェクト憲章、②コミュニケーション計画、③WBS(Work Breakdown Structure)…
-
ブログ / 1,126 views