IE手法(インダストリアル・エンジニアリング)における3つの作業測定方法について
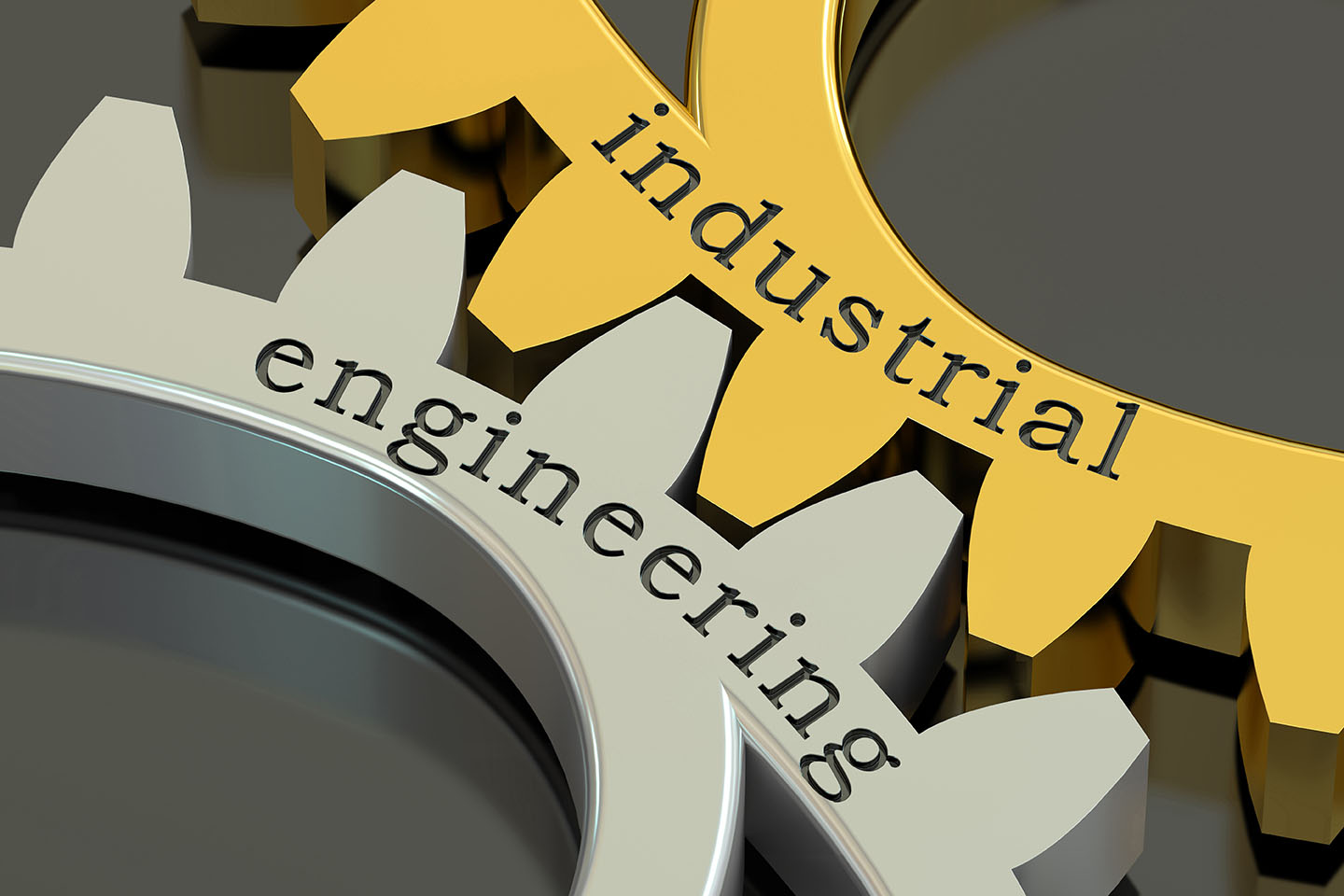
はじめに
製造業、物流業の企業において、多くの工場や倉庫が業務改善に取り組んでいます。この改善という言葉は海外でもKAIZENという英語のアルファベット表記で利用されることもありますが、その理由は日本を代表する企業であるトヨタ自動車にあります。
世界的に有名なトヨタ・プロダクション・システム、TPSとも呼ばれるトヨタ生産方式では「ジャストインタイム」、「カンバン方式」などの概念が有名です。TPSのベースとなるのは改善のマインドで、トヨタでは改善は仕事のついでに行うのではなく、仕事の中心に置かれるものだと考えられています。
トヨタでは昭和30年から業務改善のためにIE(インダストリアル・エンジニアリング)手法の教育がされており、この手法が今もなお日本の多くの製造業の現場で改善のために利用されています。今回の記事ではこのIE手法における「作業測定」「工数管理」について詳しく解説します。
IE手法(インダストリアル・エンジニアリング)とは?
ではIE、インダストリアル・エンジニアリングとはどのようなものかと一言で言うと「業務改善のためにモノと人と設備の動きを細かく見る技術」で作業研究とも言われています。
作業研究は「方法研究」と「作業測定」の2つに分けられ、方法研究は工程や作業方法、手順を分析して改善することで「作業測定」は作業に必要な時間を測定して無駄な時間の排除、標準時間の設定を行ないます。標準時間というのは標準的な熟練度の作業者が標準の作業方法や条件のもと作業を行った場合にかかる作業時間に余裕時間を加えた時間のことです。
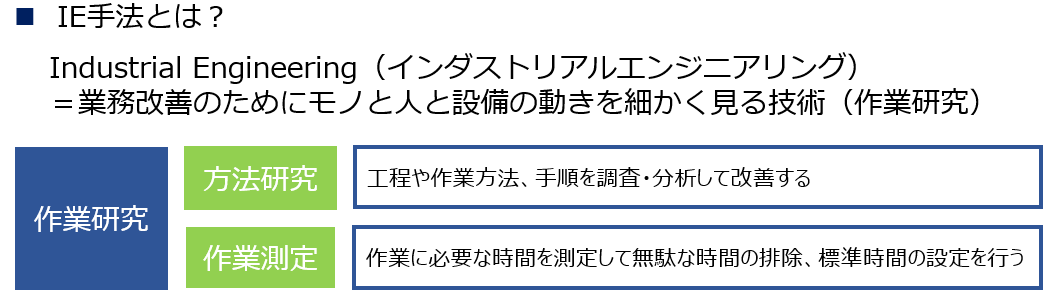
図①:「IE手法」
作業測定において、ある作業が完了するまでに必要な人数・時間を表す指標のことを工数と呼んでおり、工数の測定方法は3種類あります。一つ目は仕事をビデオ撮影して連続して分析する「連続時間分析法」。二つ目は工場あるいは倉庫の管理者がストップウォッチを使って部分的に仕事を抜き取って計測する「ワークサンプリング法」。3つ目は作業者が作成した一定期間の作業日報を集計して行う「セルフタイムスタディ法」です。
この3つの測定方法にはそれぞれメリットとデメリットがあります。まず連続測定法のメリットですが、ビデオ撮影なので秒単位の正確な時間が測定できます。デメリットは1台のカメラではビデオの画角に収まる人数の計測しかできないので、人数が多い場合は複数のカメラ、撮影者が必要で撮影後のデータ分析にも時間がかかります。
ワークサンプリング法のメリットは管理者1名がストップウォッチを使って一定の時間間隔で複数の作業者を一度に計測できる点です。デメリットはこれもビデオ撮影と同じく、一人の人が目視できる作業者の数は限られているので、人数が多い場合は人手が必要で、計測後のデータ集計に時間がかかる点です。
セルフタイムスタディ法のメリットは作業者が自分で作業時間を記録するので、調査のために特別な人手が不要な点です。デメリットは自分に都合が良いように記録してしまうことがあるので、必ずしも正しい記載とは言えない点です。
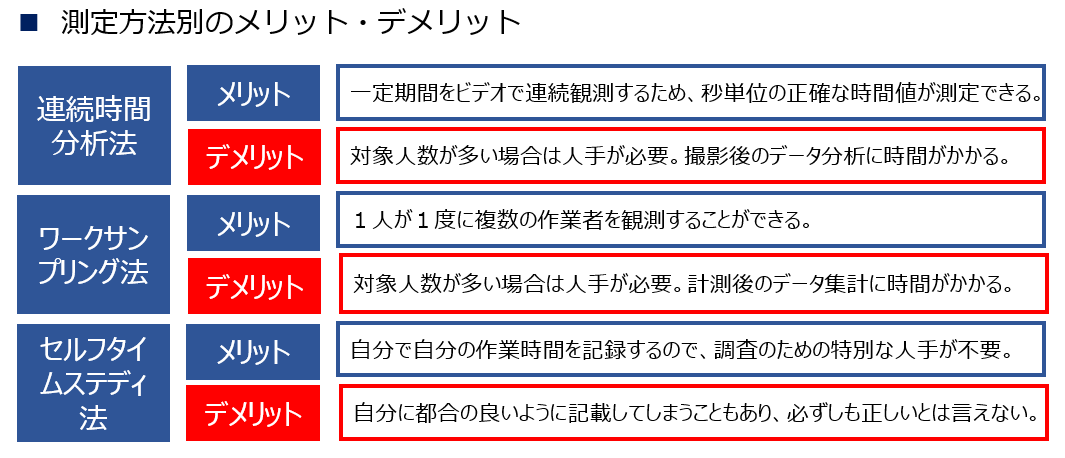
図②:「測定方法別のメリットとデメリット」
それぞれの測定方法でメリット、デメリットがありますが、一般的に社内の改善チームや外部コンサルタントによる短期計測の場合はビデオ撮影者を立てた連続分析法やストップウォッチを使うワークサンプリング法が利用されることが多いです。
一方現場スタッフによる業務改善で長期に渡る計測が必要な場合は作業者自身が書いた手書き日報によるセルフタイムスタディ法が利用される傾向があります。
セルフスタディ法による工数管理の課題
ではこれからセルフタイムスタディ法で機械と人の作業内容の測定をしていた会社が抱えていた工数管理の課題について説明します。
精密加工部品の製造会社A社の工場には120の製造ラインがあり、この工場で生産している精密加工部品の点数は1,000アイテム以上、毎日約150名の作業者が勤務しています。
この会社は冒頭で説明したトヨタ生産方式で業務改善を行なっていて、工数管理のためにラインごとの稼働実績表を作業者が手書きで作成し、前日の120枚の手書きの稼働実績表を改善チームがエクセル入力して正味(しょうみ)稼働時間の工数の算出をしていました。
課題はラインが120もあるので、毎日120枚の手書きの稼働日報を150名の作業者が手書きで作成するのに手間がかかることと、その手書きの稼働日報を業務改善チームがエクセル入力して集計するのに時間がかかることです。
手書きの稼働日報に書き間違いや読めない文字もあり、その確認作業にも手間がかかるのが課題になっていました。こちらがそのラインごとの稼働実績表です。
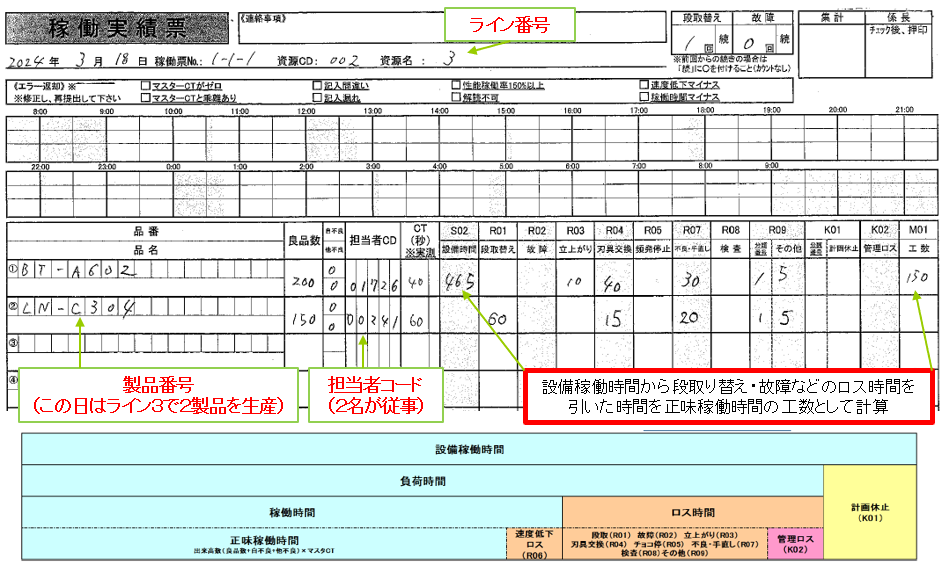
図③:「手書きの稼働実績表」
ラインごとにその日に生産した製品番号とその生産に関わったスタッフのコード、ラインの稼働時間と段取り替えや故障などでラインを止めていた時間を手書きで記入していました。この日は3番目のラインで2つの製品の生産をするのに2名の作業者が関わっていました。
ラインの数は120なので毎日120枚の手書きの稼働実績表が作成されます。業務改善チームの担当者は毎日前日の120枚の稼働実績表をエクセル入力して、機械の正味稼働時間、生産ロス時間を算出して、標準時間通りの生産ができたいたかどうかを検証します。
ご想像できるかと思いますが、作業工数を管理するために作業者、業務改善チームの担当者ともに多くの手間と時間を割かなければいけません。この課題に対してDX(デジタル・トランスフォーメーション)を使って何とか解決できないだろうか、と業務改善チームの担当者は考えました。
DXを使ったラインごとの工数管理の可視化
業務改善チームの担当者はインターネット検索をして、「イプロス」という製造業界のBtoBマッチングサイトに掲載されていた作業時間をスマートフォンやタブレットで計測するツール「じょぶたん」を見つけました。
このツールは当社NX総合研究所が開発したもので、タブレット利用の場合は作業内容が変わるタイミングでタブレットに表示されている作業項目のボタンを押した後にIDカードあるいはQRコードをかざすことで、作業内容と作業時間、作業したスタッフをかんたんに記録できるツールです。
NX総合研究所によるオンラインデモで「じょぶたん」の詳細説明を聞いた業務改善チームの担当者はラインごとにタブレットを設置して、作業者が各ラインで作業をする時にスタッフIDのQRコードと製品番号のQRコードを読み取りさせれば、稼働実績表に記載している「ラインごとの機械の正味稼働時間」、「故障ロス時間」、「生産した製品番号」と「対応したスタッフ」の情報が一度に把握できると考えました。
こちらがタブレットの画面です。ラインごとに2画面あり、1画面目の左上に「設備稼働」というボタンがありますが、ラインが正常に動き始めたらこのボタンを押します。
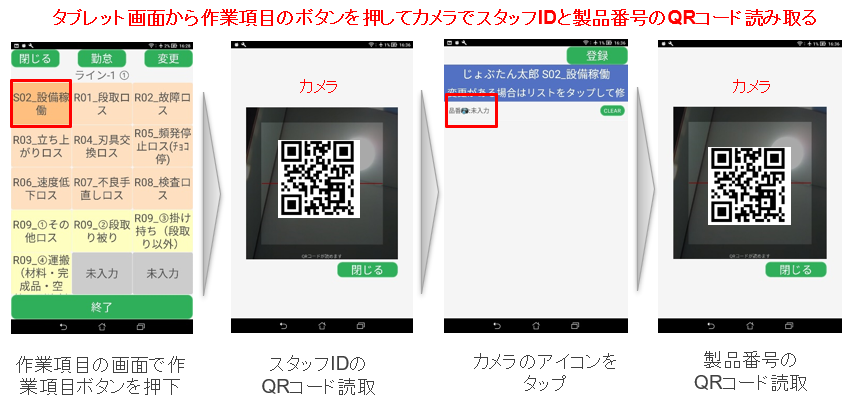
図④:「じょぶたんタブレット画面」
ボタンを押した後にスタッフIDを読ませるカメラの画面が表示されるのでスタッフIDのQRコードを読ませます。その後で製品番号のQRコードを読ませるために「カメラ」のアイコンを押すとカメラが起動するのでここで製品番号のQRコードを読ませます。ここはバーコードを読ませることも可能です。
この動作によってライン番号、機械の稼働開始時刻、生産した製品の製品番号、対応したスタッフの情報が一度に記録できます。サーバーにアップロードされたデータは管理者は「じょぶたん管理者用Webサイト」からすぐにダウンロードして、「ラインごとの機械の正味稼働時間」、「故障ロス時間」などの算出を行うことができます。
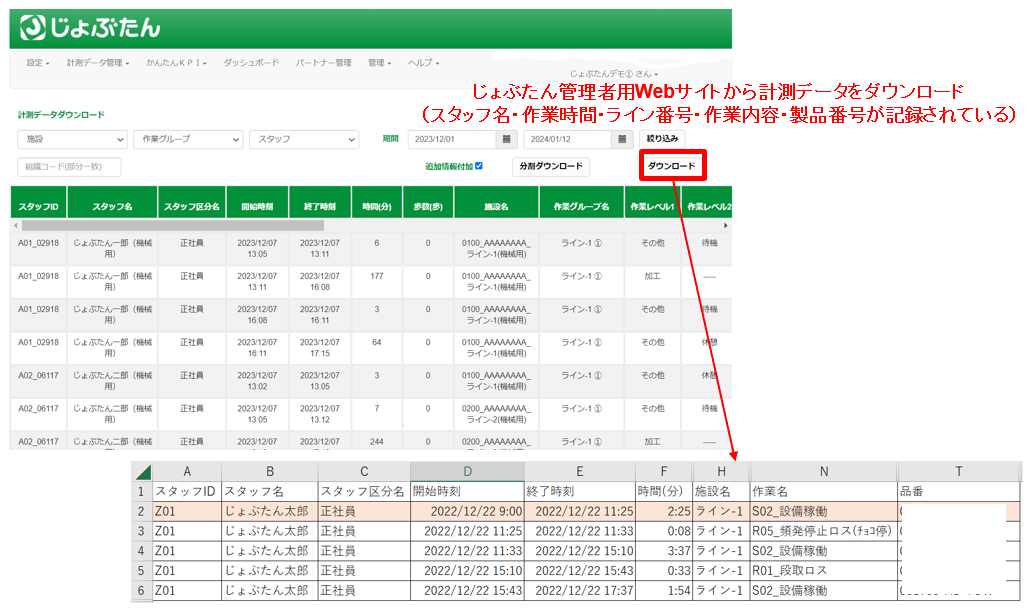
図⑤:「じょぶたん管理者用Webサイト」
おわりに
「じょぶたん」の利用によってラインごとの設備稼働状況がデータ化されたので、現場作業者は稼働実績表に手書きで機械の稼働時間、故障ロス時間を書く必要がなくなりました。また業務改善チームによるエクセルの入力と集計作業もなくなりました。
「セルフスタディ法」による工数管理でかかっていた手間と時間を大幅に削減することができた上に、手書きによる書き間違いがなくなり、工数の見える化の精度と効率が大幅にアップしたとのことです。
冒頭で申し上げた通り、IE手法とは「業務改善のためにモノと人と設備の動きを細かく見る技術」です。以前は人手や手間をかけてやっていたIE手法ですが、昨今ではDXを利用することでより簡単に精度の高い見える化を実現できるようになりました。
トヨタ生産方式のIE手法を導入している製造現場、物流現場において、作業工数取得に苦労しているという課題がありましたら、DXソリューションを検討してみるのはいかがでしょうか?
作業時間計測ツール「じょぶたん」
この記事内容に関連したお役立ち資料「改善の源流となるIE手法について」のダウンロードページ
(この記事は、2024年2月26日時点の状況をもとに書かれました。)
掲載記事・サービスに関するお問い合わせは
お問い合わせフォームよりご連絡ください
福井 康雅が書いた記事
-
ブログ / 1,057 views
-
ブログ / 1,140 views物流ドローンが変える未来 ~ドローンによる建設資材運搬の実証実験レポート~
物流ドローンが日常的に空を飛んでいる未来を少しでも早く実現するための実証実験は全国で活発に行われています。兵庫県姫路市で行われた「物流ドローンによる登山道整備の…
-
ブログ / 1,086 views利便性・安全性を更に高めたモーダルシフトの実現を目指して!~大阪-札幌間の鉄道貨物輸送試験レポート~
CO2排出量の削減に大きな効果があり、SDGsの観点から多くの企業が取り組んでいるモーダルシフト。1トンの貨物を1km運ぶ際に排出するCO2がトラックの11分の…
この記事の関連タグ
関連する記事
-
ブログ / 646 views
-
ブログ / 702 views理論在庫(適正在庫)算定のかんどころ
理論在庫(適正在庫)の算定について、巷の教科書的な資料を補足する視点で安全在庫を主体に語っています。巷の解説資料でも計算式自体はたくさん記載があるので、計算する…
-