物流倉庫の在庫が合わない理由と改善策
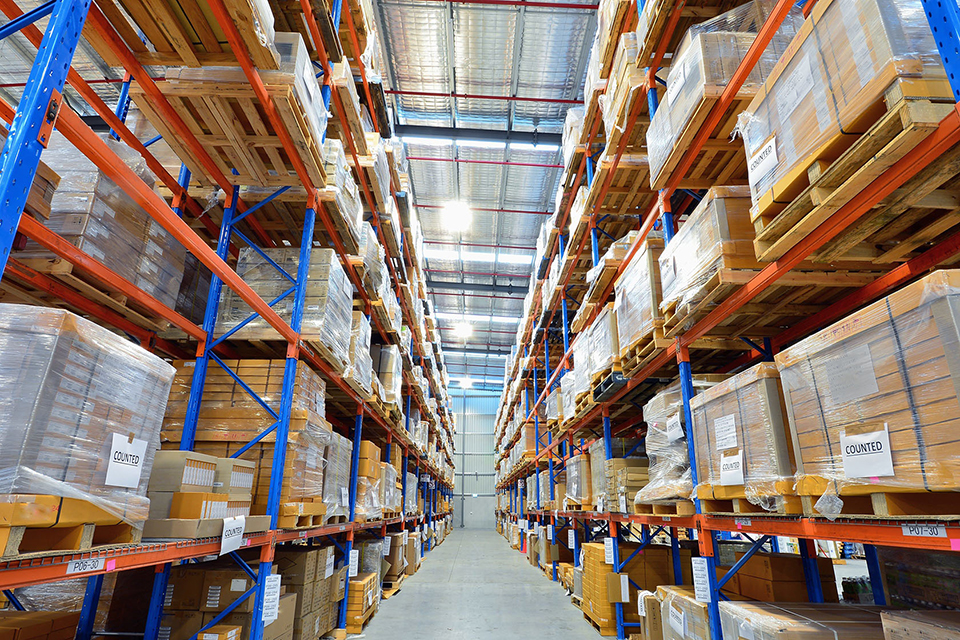
目まぐるしく物が流れる倉庫内で、在庫差異ゼロは一つの大きな課題です。在庫差異によって、①資産の減少、②顧客信頼性と満足度の低下、③作業生産性の低下という3つの弊害が発生します。では、なぜ在庫が合わないのかという理由については、主に①事務での入力ミス、②倉庫での作業ミス、③仕入れ先のミスの3つが考えられます。そして、こうした人的なミスを低減させる手法としては、①システムの構築と②ロケーションの管理徹底があります。以下、詳細についてご説明いたします。
在庫差異による弊害
在庫が合わなくても特に問題が無ければ労力をかける意味はありませんから、先ずは在庫が合わないことによる問題は何かを知ることから始めます。
一つめに資産の減少が挙げられます。企業のおカネがモノに変わった存在、それが在庫です。その在庫が合わない、失われるということは、すなわち会社の資産の減少を意味します。自分の稼いだお金で買った車や家がある日突然理由も無く消滅している。在庫が無くなるということはそういうことです。
二つめに顧客信頼性と満足度の低下が挙げられます。データ上在庫があれば受注までは処理されますが、実在庫が無ければ出荷できません。つまり納品を期待していた顧客に物が届かず、信頼性が失われる結果になってしまいます。
三つめに作業生産性の低下が挙げられます。在庫が合致していれば何の問題無く流れるフローも、在庫差異によって無駄な作業が発生します。ピッキングに行った棚へ商品が存在しない。慌てて商品を捜索する。商品が見つからない場合は顧客と調整しなければならず、クレームになった日にはその対応に迫られる。と、全てが悪い方向へ流れてしまいます。
在庫が合わない主な理由
各企業によって細かな場所は異なりますが、大きく括ると人的な処理ミスによって在庫は合わなくなります。在庫差異がよく発生する箇所を3つ記載します。
一つめは事務での入力ミスです。調達によって数量を入力する時。受注の入力をする時。出荷の入力をする時。企業によっては自動化されている部分もありますが、各企業ともどこかのタイミングで入力作業が発生しているはずです。在庫に関わる入力作業は全く無いよという企業が存在するのであれば是非教えて頂きたいくらいです。この入力作業を誤ってしまうと、在庫差異が発生します。私が経験したなかで酷かったエピソードは、在庫数量をバーコードでスキャンしながら入れるフローで、商品コードを誤って入れていたというものがあります。通常10個や20個単位の数値が入る場所に、4912345678901個という桁数の在庫がスキャン入力されていました。
二つめは倉庫での作業ミスです。ピッキングで1個取るべきところを2個取ってしまう。本来あるべき棚とは別の場所に商品を保管してしまう。紛失や破損の欠減処理を怠ってしまう等が挙げられます。1A-03-3-3-1にあるべき商品が1A-08-3-3-1に置かれていたりします。
三つめは仕入れ先のミスです。発注数通りに商品が届かない場合、データ上の在庫と実在庫に差異が発生します。
在庫差異の発生を減少させる手法
上記で述べたように在庫が合わなくなる理由のほとんどは人的なミスによるものですから、このミスを如何に低減させられるかが重要なポイントとなります。その手法を2つご紹介します。
一つめはシステムの構築です。先に書いた事務作業の入力作業を減らせられる箇所があれば、人手によるミスを低減できます。指示通りの入出荷を行っているにも関わらず、後から作業指示の変更が頻発しているような倉庫は、その上位の受発注業務で入力ミスが多発している可能性が高いです。その場合、一度上位である基幹システム内の在庫に関わる入力作業を洗い出し、どこでミスが発生しているのか、また、そのミスはシステムを再構築すれば減少可能なのかを検証する必要があります。先述した数量入力箇所に商品コードがスキャンされていた例などは最たる改善ポイントです。通常であれば1日10個前後の入荷商品なのに、ある日突然4912345678901個入荷されるという情報がきたら驚きますよね。そんな入力ミスがミスのまま流れるフローは放っておいてはいけません。
二つめはロケーションの管理徹底です。分かり易いロケーション管理ができているかどうかは、入出荷作業の精度を左右する重要なポイントです。倉庫内の住所といえるロケーションは、エリア-列-連-段-間口という階層で数値を使用して分けていく手法が一般的です。倉庫内の大きさや間口の取り方によって省略する箇所もあります。
まとめ
在庫差異によって、①資産の減少、②顧客信頼性と満足度の低下、③作業生産性の低下という3つの弊害が発生してしまいます。このような在庫差異は、主に①事務での入力ミス、②倉庫での作業ミス、③仕入れ先のミスの3つ人的なミスが理由となっています。ですから、こうした人的なミスを低減させるためには、①システムの構築と②ロケーションの管理徹底という手法が有効となるわけです。
物だけが行き来していた時代と異なり、今は情報と物が別々に動いております。信頼に足る情報にできるかどうかは倉庫作業の管理によるところが大きいといえるでしょう。
掲載記事・サービスに関するお問い合わせは
お問い合わせフォームよりご連絡ください
NX総研編集部が書いた記事
-
ブログ / 823 views(物流2024年問題)ラストワンマイルデリバリー改革に向けたスモールスタート
「物流の2024年問題」を端に発し、政府、各物流関連団体などが連携した継続的な情報発信により露出も増え、物流事業者以外の企業、また、物流サービスのユーザーである…
-
ブログ / 933 viewsスイス・ヌーシャテルの交通事情: 持続可能な交通システムと地域の取り組み
スイスは、持続可能な交通システムの開発において先駆的な国です。以下では、スイスの交通システム開発に関する状況を分析し、私が訪れたヌーシャテル市を事例に、その特徴…
-
ブログ / 1,907 views
この記事の関連タグ
関連する記事
-
ブログ / 520 viewsアサーション:物流現場でも使えるコミュニケーションスキル
「アサーション」とは、「自分も相手も大切にする自己表現」で「自分の考え、欲求、気持ちを、率直に、その状況にあった適切な方法で伝えるスキル」です。 アサーションを…
-
ブログ / 1,450 views物流案件を進める上で必要なプロジェクト・マネジメント スキル
プロジェクト・マネジメントに有効なスキルツール、主には①プロジェクト憲章、②コミュニケーション計画、③WBS(Work Breakdown Structure)…
-
ブログ / 1,126 views