【倉庫改善】IoTを活用する!デジタル社会における倉庫改善事例
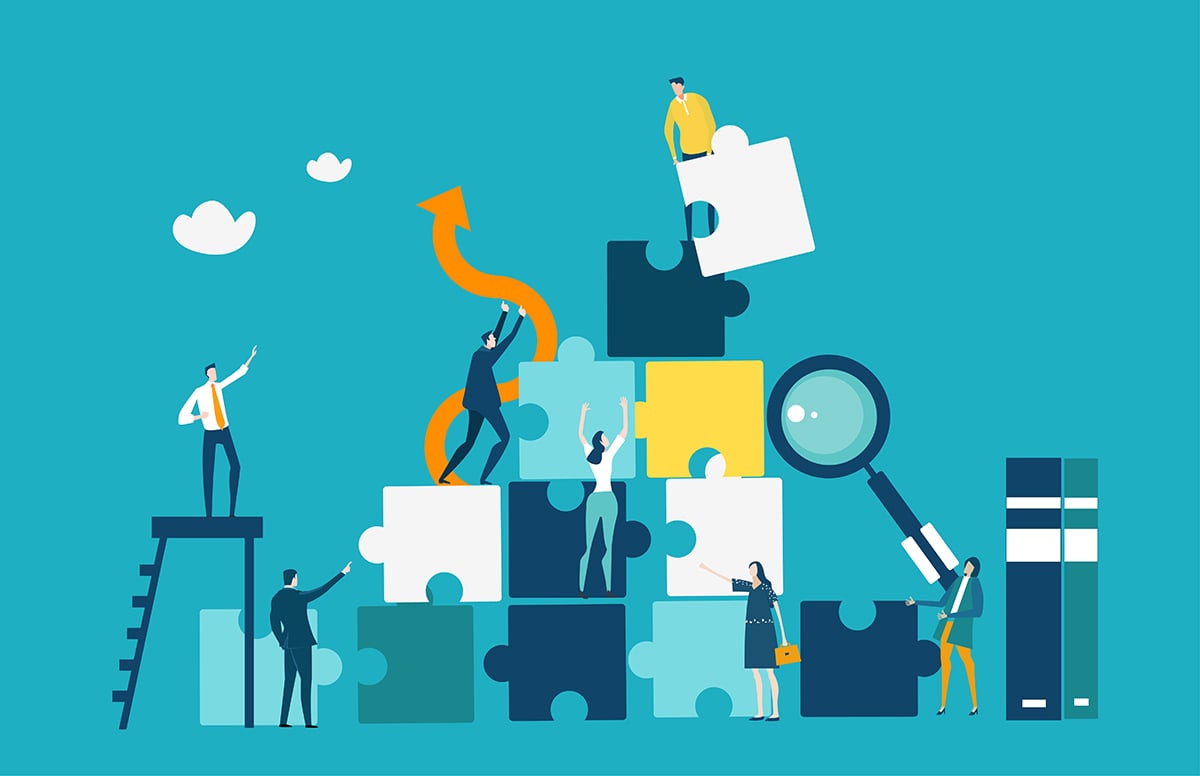
デジタル社会の到来
ニュースや紙面で、IoTやAIというキーワードを目にしない方が珍しい日々が続いています。物流現場においても経営層から管理者に対して「現場改善を目的としたIoTやAIの活用を検討するように」といった宿題が与えられるケースが増えていることでしょう。
デジタル社会の到来により外部環境が大きく変化する中、データを駆使した客観的な現場改善の重要性は増しています。一方で、現場改善の基本的な考え方は従来と大きく変わることはありません。IoTで大きく変わる部分は、現状を把握するスピード、精度、それに要する費用です。現状把握フェーズはIoTでスマートに行い、取得したデータに基づく客観的な分析は、現場改善を担当するスタッフがじっくりと考えることが必要です。アパレル通販の倉庫改善事例を通じて、IoTから改善を実践する手法を紹介します。
見える化手段の多様化
倉庫の改善を前提とした代表的な見える化として、「作業時間の見える化」と「動線の見える化」の2つのアプローチがあります。これらを「直接的な見える化」とします。更に、直接的な見える化を使い、生産性などの「間接的な見える化」へ加工することも必要となります。
「作業時間の見える化」は、作業時間を限られたリソースやコストとして捉え、時間の使い方(コストの使い方)が上手く行えているか否かを分析・検証します。一方、「動線の見える化」は、運搬や歩行を出来るだけ短くする、または昨今であればAGVやAGFまたはピッキングロボットへのシフトを前提に、抜本的な生産性の向上や将来的な人手不足への備えを分析・検証します。
作業時間の見える化IoTソリューション
作業時間の見える化IoTソリューションとして「ろじたん」があります。「ろじたん」は日通総合研究所が開発したスマートフォンやタブレットを使って作業時間を計測するツールです。作業スタッフ自身がスマートフォンやタブレットに対して定期的に作業を登録することで、高い精度で現場の作業を見える化することができます。
2015年10月よりサービスを開始してから4年半で約350拠点へ導入致しました。この分野では、物流業界で最も利用されているソリューションといえます。「ろじたん」は、WEBシステムとスマートフォンやタブレットとの連携によるクラウドサービスであり、機材は必要な期間、必要な台数をレンタルすることが出来ます。そのため、日々のパフォーマンスチェックはもとより、改善を目的としたBefore/After検証を行うことも可能となっています。手軽かつ低コストで利用できることから、10名程度の小規模な倉庫から1,000名程度の大型倉庫まで、様々な規模の倉庫で利用されています。
作業動線の見える化IoTソリューション
作業動線の見える化では、カメラによる画像解析のイメージが強いかもしれません。広いエリアで作業する物流現場では、設置するカメラ台数や解析ソフトを考えるとコスト面で少々状況が変わります。現状把握フェーズは、一般的に大きなコスト負担が難しいフェーズといえます。そのため、現時点で動線を取得する手段の本命はBLE(Bluetooth Low Energy)ビーコンを利用した方式が望ましいと考えます。BLEビーコンのイメージが湧かない方は、低消費電力でBluetoothの信号を一定間隔(0.1秒~1秒程度)で発信する小さな箱とイメージして下さい。この箱を作業現場のポイントとなる場所に設置したり、10m程度の一定間隔に設置することで、スマートフォン等の受信装置を保有する作業スタッフの動線を簡単に取得できるようになります。
主なソリューションとして、ゼンリンデータコム社の屋内動態管理ソリューションやマルティスープ社のiField indoorがあります。BLEビーコンに関しては、GPSでは難しい屋内の位置情報の取得を中心に、今後も様々なソリューションの登場が期待されています。
改善活動の7つのステップとケーススタディ
デジタル社会が大きく進展する中でも、現場改善の基本的な進め方は、従来からいわれている7つのステップが基本となります。日通総合研究所でも、表1の7つのステップで実施することを推奨しています。現場改善は、基本手順を踏まえた上で、自分たちで考えて行動することがポイントとなります。改善ツールは基本手順の推進をサポートする道具となります。これまでは、現状把握で作業時間や動線を把握することは、現場や管理者の負担が大きく非常に困難な工程となっていました。現在は、先に紹介したようなIoTやITソシューションの進展により、低コストかつ高精度で現状把握(見える化)を行うことが可能となっています。
表1.7つのステップ
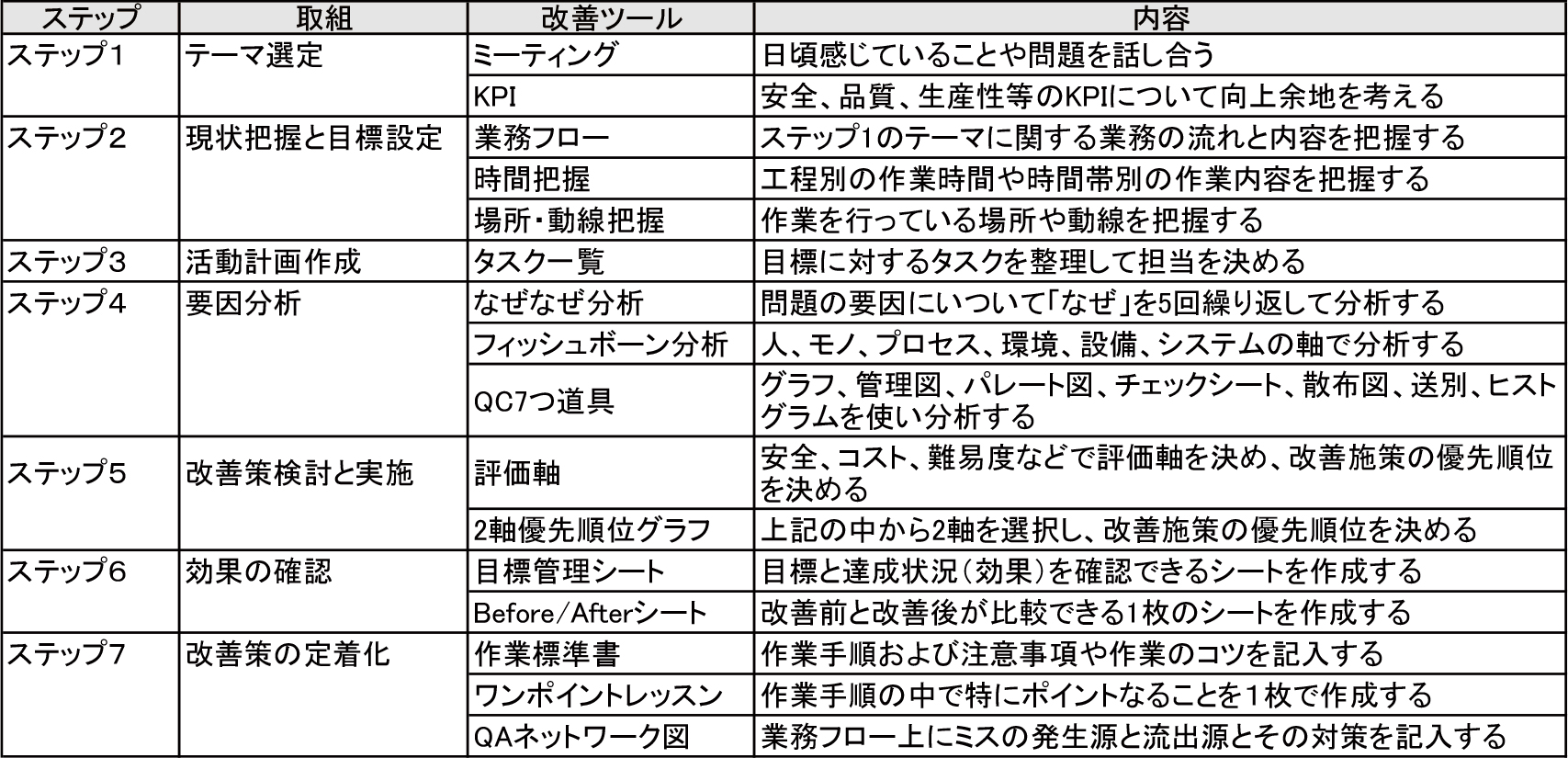
出典)日通総合研究所 ろじたん お役立ち資料「改善活動は基本7ステップと支援体制が成功への近道」P2の図表に筆者加筆作成
表1の7つのステップを実際のケーススタディを通して理解を深めて欲しいと思います。ケーススタディの対象として、アパレルの通販センター(A社)を取り上げます。A社は、出荷物量が年間120%の増加にあり、受注したオーダーを翌日出荷するサービスレベルを何とか死守していました。しかしながら、昨今の人手不足の影響もあり、サービスレベルの維持が難しい状況となり、改善活動に取り組むこととしました。
ステップ1:テーマ選定
現行の作業スタッフでサービスレベルを維持するためには、生産性向上は不可避であり、メンバーで話し合った結果、テーマとして「①倉庫オペレーションの生産性の向上」、「②誤出荷の削減」の2つを決定しました。誤出荷を入れた理由は、生産性を向上させるだけでなく、現在、月に2~3件発生している誤出荷が、手戻りとして生産性へも影響を与えていることから、一緒に考える良い機会として捉えたことにあります。KPIについては、これまで取得していなかったことから、今回の取り組みで新たに仕組みを構築することとしました。
ステップ2:現状把握と目標設定
倉庫オペレーションの生産性をきちんと取得するために、管理すべき(管理したい)生産性を検討し、それが取得できる粒度で作業時間の把握を行いました。現状把握のソリューションとしてスマートフォンを使う「ろじたん」を採用しました。これは15分に1回スマートフォンから通知があり、そのタイミングで自分の行っていた作業をスマーフォン画面からタッチして記録するというものです。通知のタイミングで入力するため、その時間帯に行っていた作業を確実に記録することができる仕組みとなっています。
生産性の向上には作業動線の把握も必要と考えましたが、「ろじたん」では作業工程別の歩数も計測することができるため、それで代替することしました。特に、ピッキングで1アイテム(ピッキングリストの明細1行)取るのに何歩費やしているのかを把握することを意識しました。各工程の作業時間の結果は図1の通りでした。
梱包と出荷検品で全体の約21%を要しており、優先的に改善すべき工程であることが分かりました。ピッキングについても2Fと3Fで同じくらいの時間を要しており、各フロアに作業が分散していることが把握できました。歩数については、1行ピッキングするのに35歩を費やしていました。これらの作業時間をベースとして、①倉庫全体生産性(オーダー数/休憩を除く全作業時間)、②ピッキング生産性(行数/ピッキング作業時間)、③検品・梱包生産性(オーダー数/検品・梱包時間)の3つの生産性指標を把握することにしました。オーダーの多くは単品購入のため、オーダー数≒梱包数と見なすことが出来ると判断しました。
図1.作業時間比率
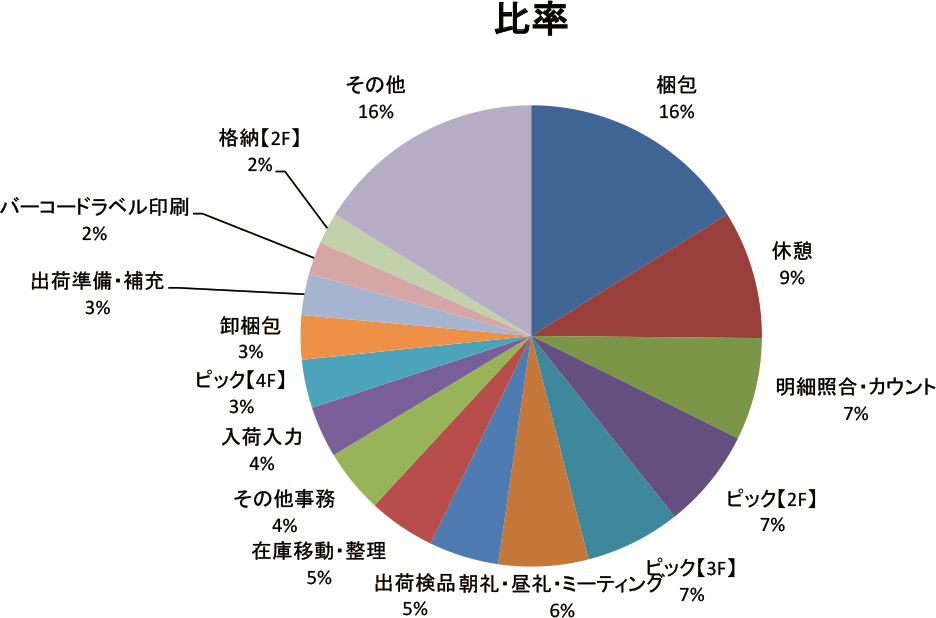
出典)筆者作成
現状の結果を踏まえ、ピッキング、出荷検品、梱包工程について、簡単な業務フローを作成しました。図2は、出荷検品と梱包の業務フローとなります。出荷検品は2名で読み合わせを行い、出荷検品と梱包間でローラー上に仮置きしていることが分かります。このように、業務フローから非効率な工程が明らかになります。
現状把握の結果から活動で目指す目標を設定します。ここでのポイントは、目標は可能な限り高く設定することにあります。本活動でも、ピッキングと出荷検品・梱包工程の10%の生産性向上、2~3件/月発生している誤出荷をゼロにすることを目標としています。
図2.出荷検品と梱包の簡易業務フロー
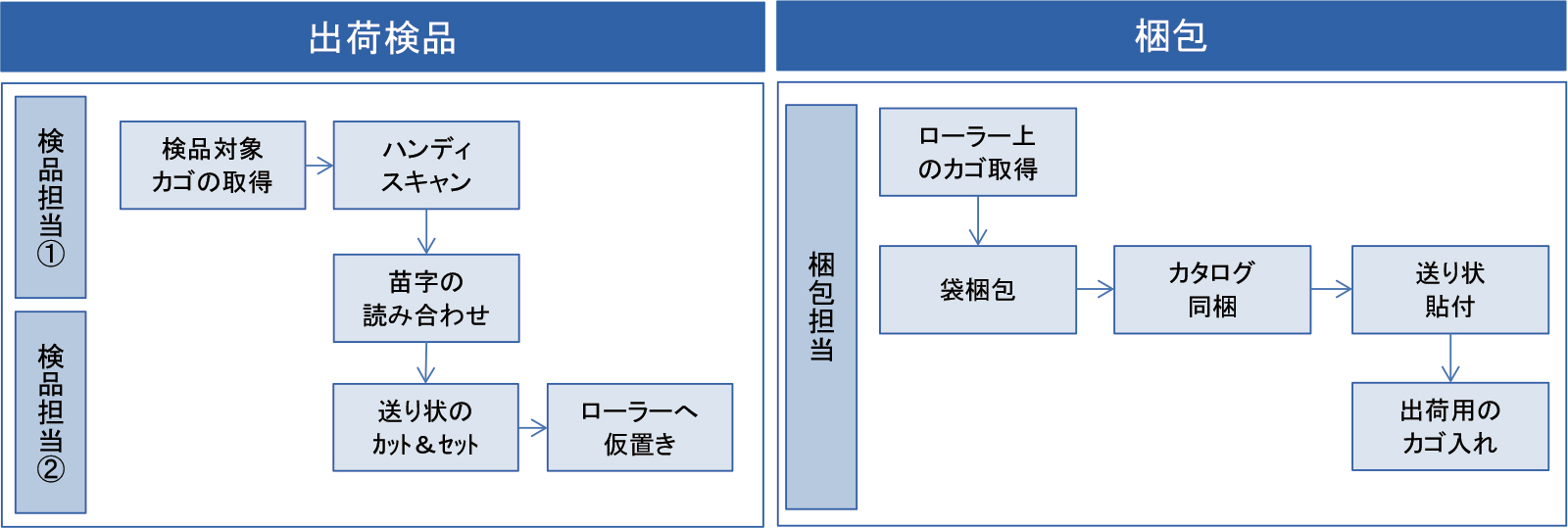
出典)筆者作成
ステップ3:活動計画作成
①ピッキング作業の生産性向上、②出荷検品・梱包作業の生産性向上、③誤出荷ゼロ、をテーマとして再設定し、更に各テーマにステップ4~7の実施スケジュールを活動計画として作成しました。今回のケースでは、①~③の各テーマが相互に影響していることから、分業制ではなく、全員で課題の要因や解決策のアイデア出しを行い、1名の担当が整理して検討する方式としました。
ステップ4:要因分析
出荷検品と梱包作業に対しての要因分析は「なぜなぜ分析」を使用しました。その結果、出荷検品と梱包で時間が掛かっているのは、分業により受け渡しや仮置きが発生していることが要因で、梱包作業台6台に対して、送り状のプリンタが2台しかないというハード的なことが起因していました。そのため、前工程として出荷検品を行い、検品と同時に印刷される送り状と納品書をセットにしてから、後工程の梱包工程に流さざるを得ないことが分かりました。この要因分析のやり方には、フィッシュボーン(特性要因図)の利用や、QC7つ道具(散布図やパレート図等)があり、分析のアプローチにより使いやすいものを選択して下さい。例えば、生産性のバラツキ具合を検証する際には、物量と生産性を2軸とする散布図を使う、在庫数量や出荷頻度の検証にはパレート図を使うなどが考えられます。
表2.なぜなぜ分析
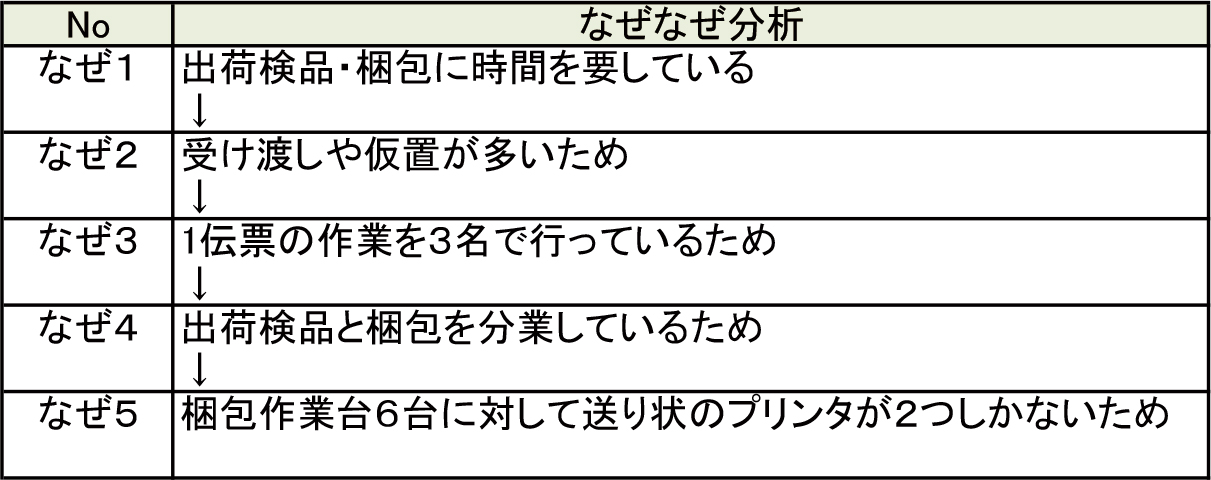
出典)筆者作成
ステップ5:改善施策の検討と実施
レイアウトで想定していたよりも多くの歩数(1行あたり35歩)を費やしていたため、商品を探している歩数が余計に生じていることが分かりました。ピッキング作業の生産性を向上するためには、これまでの棚の品番、サイズ、カラー番号による間口管理を廃止して、ロケーション番号による間口管理へ切り替える必要があると考えました。更に、固定ロケーションからフリーロケーションにすることで保管効率の向上を図ると同時に、ピックエリアを再編することにしました。具体的には、2Fに出荷頻度の高い商品を集中的に保管することで動線の短縮を図っています。
出荷・検品工程については、図3の通り、送り状のプリンタを増設して梱包工程に置くことで、出荷検品と梱包工程を一体化し、1名の作業スタッフによる完結方式へ変更することとしました。1名作業かつ1伝票毎の作業とすることで、梱包工程による入れ間違いによる誤出荷も防止することができます。
施策の実施については、費用と効果の2軸で4つのマトリクスを作成して検証しました。ピッキング工程の改善と出荷検品・梱包工程の改善は、「少ない費用で大きな効果」の分類に入り、優先度の高い施策であると評価しました。
図3.出荷検品・梱包工程の改善施策
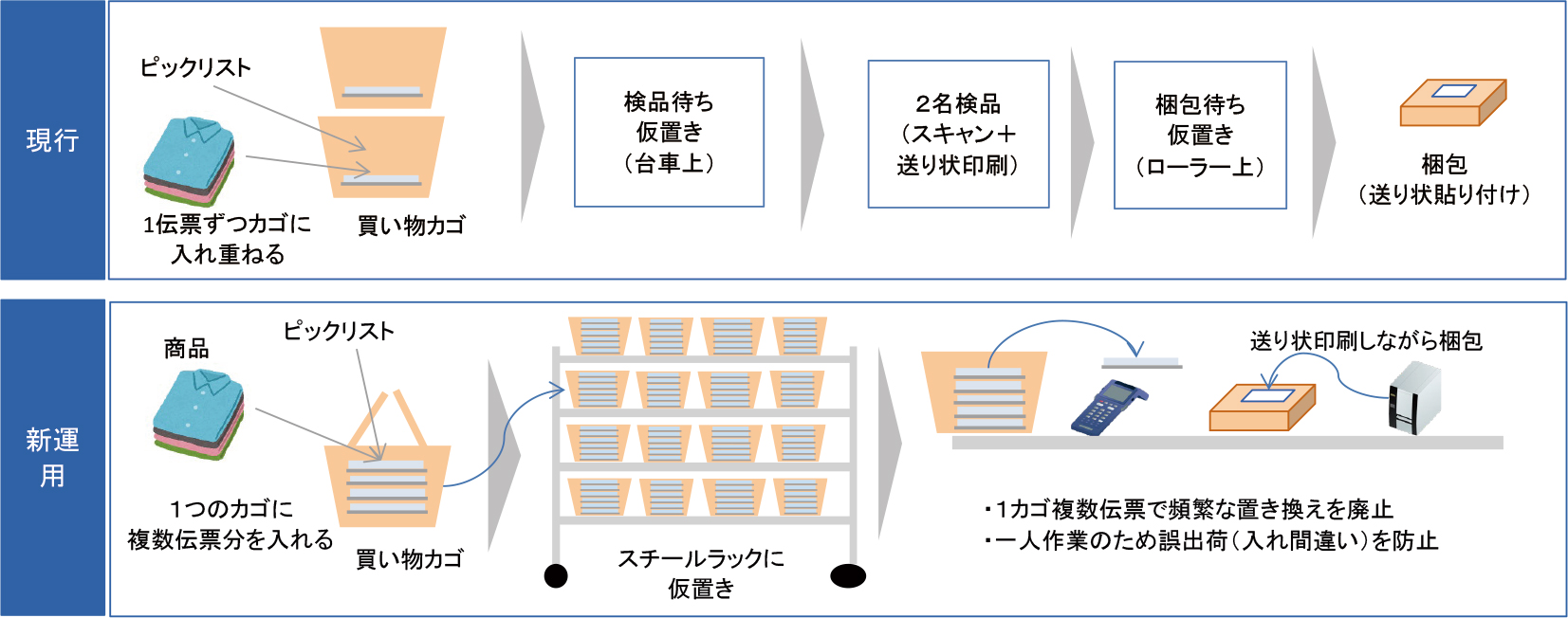
出典)筆者作成
ステップ6:効果の検証
改善施策を導入してから3カ月後に、再度「ろじたん」を使い改善後の作業時間と生産性の把握を実施しました。結果は表3の通りでした。出荷検品と梱包工程を一体化したことから、ムダな仮置きや読み合わせ作業が不要となり40%を上回る生産性の向上に繋がりました。
ピッキングに関しても、ロケーション管理を導入し、出荷頻度の高い商品を2Fに集約したことで7.3%の向上となりました。ピッキング歩数も1行あたり35歩だったものが18歩まで短縮され約半減となりました。
月間の誤出荷件数についても3件から1件の発生に削減しました。最も重視した倉庫全体生産性は15.9%と大幅な改善となり、改善活動は成功を収めました。表3のような目標管理シートを作成することで、過去の推移と目標に対する現在地を常に確認することができます。
表3.目標管理シート
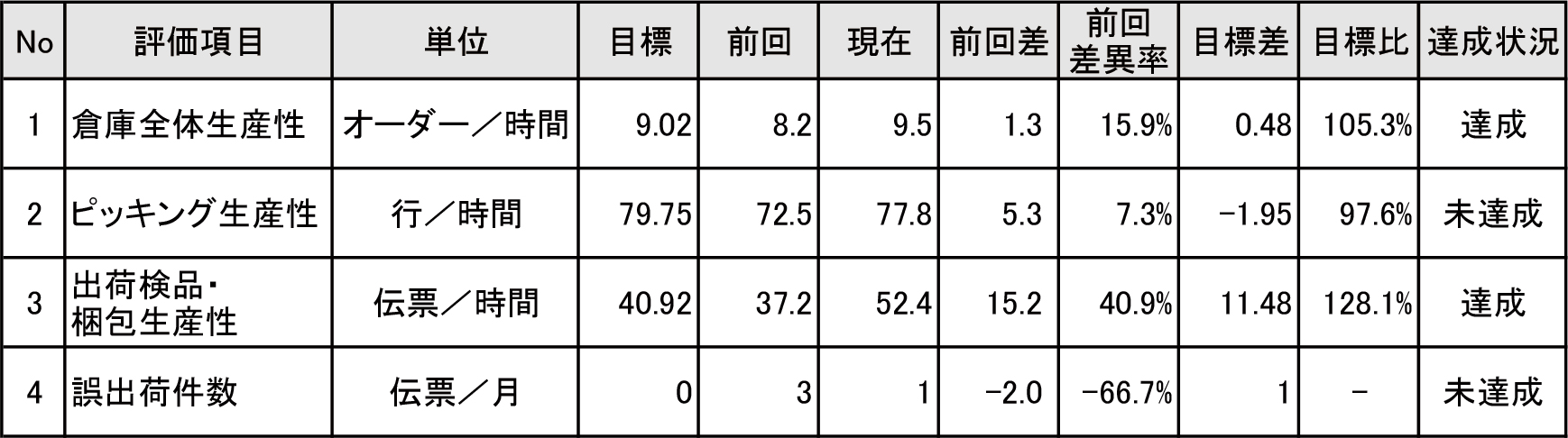
出典)筆者作成
ステップ7:改善策の定着
改善施策を一過性のものとしないために、改善施策を定着させる必要があります。作業標準書(マニュアル)やワンポイントレッスンはそのための重要なツールとなります。作業標準書は各作業パートが1枚で完結するようにシンプルに記入し、注意事項やポイントを赤字や写真・図を使い、初めて作業を行うスタッフにも理解できるようにすることが重要となります。ワンポイントレッスンに関しては、特にポイントとなる部分のみを抽出して現場に貼りだすことで、事故やミスの防止に大きな効果を発揮します。定着化を目的とするツールの最大のポイントは「誰が見ても容易に理解できること」といえます。
おわりに
改善活動を成功させるには、改善を検討するメンバーが常に最善を「追求」かつ「継続」して行うことが重要となります。高いモチベーションで現場改善をスタートしたものの、日々の業務に忙殺され、徐々にモチベーションが下がってしまうということが往々にして起こっています。改善活動を推進するメンバーレベルでは、確保できる時間や予算に限界があります。
つまり、マネジメント層(場合によっては経営層)の関わり方次第で、その成否は大きく変わってくるといえます。重要なのはマネジメント層が改善活動を全体に宣言・周知してきちんと評価することです。これだけで改善メンバーは「会社が自分をきちんと見てくれている」との意識に変わります。
一方で、マネジメント層が改善活動にあれこれ関与することは不要と考えます。改善活動は、自分で考え実行することに意義があります。マネジメント層は、改善活動が円滑に行える環境作りに徹して、現場活動のサポーターとなることで、メンバーのモチベーションは飛躍的に向上します。
従来の7つのステップを踏襲しながらも、IoTをはじめとする新しい技術の活用は不可避となっています。これらを駆使ながらチャレンジし続ける現場改善が次なるステージへ飛躍すること期待します。
(この記事は2020年4月30日の状況をもとに書かれました。)
作業時間の見える化IoTソリューション「ろじたん」はこちら
掲載記事・サービスに関するお問い合わせは
お問い合わせフォームよりご連絡ください
井上 浩志が書いた記事
-
ブログ / 1,621 views失敗しない物流情報システム導入のポイント! (序章)
情報システムの開発や導入に関わるトラブルを回避するためにはポイントを押えた上流工程が欠かせません。特に上流工程といわれる要件定義と基本設計は、現状の正しい理解と…
-
ブログ / 10,167 viewsトラック運賃のトレンドをいち早くキャッチしよう!【原価・実勢運賃編】
荷主企業や運送事業者は、運賃に影響を与える要因の動向をいち早く客観的に捉えることが求められます。双方の立ち位置における運賃変動への対応力の強化を目指したブログ、…
-
ブログ / 2,776 viewsトラック運賃のトレンドをいち早くキャッチしよう!【労働力編】
ドライバー不足等から高騰が予想されるトラック運賃への対策は、避けて通ることができない課題です。荷主企業や運送事業者は、双方の立ち位置における対応力を強化するため…
この記事の関連タグ
関連する記事
-
ブログ / 527 viewsアサーション:物流現場でも使えるコミュニケーションスキル
「アサーション」とは、「自分も相手も大切にする自己表現」で「自分の考え、欲求、気持ちを、率直に、その状況にあった適切な方法で伝えるスキル」です。 アサーションを…
-
ブログ / 1,453 views物流案件を進める上で必要なプロジェクト・マネジメント スキル
プロジェクト・マネジメントに有効なスキルツール、主には①プロジェクト憲章、②コミュニケーション計画、③WBS(Work Breakdown Structure)…
-
ブログ / 1,131 views